The dredging industry uses a lot of energy and most of its requirements still depend on fossil fuels. Climate change requirements, increased energy costs and product demand are major factors pushing the dredging industry to adopt energy-efficient technologies and energy-saving techniques.
Here are 10 tips to reduce your carbon footprint on dredging projects and take responsibility for your emissions.
1. Select Energy Efficient Equipment and Methods
Calculate the fuel consumption and CO2 emissions of the equipment mobilised to site and consider using equipment that is more energy-efficient.
Tip: Calculate the Specific Energy Consumption (SEC), which is a ratio between energy used and production. The SEC makes it easier to compare options and identify the most energy-efficient ones. The figure below shows the SEC for several mixture densities and discharge pipeline length calculated using i2D’s upcoming Pumps and Pipeline (PnP) tool version.
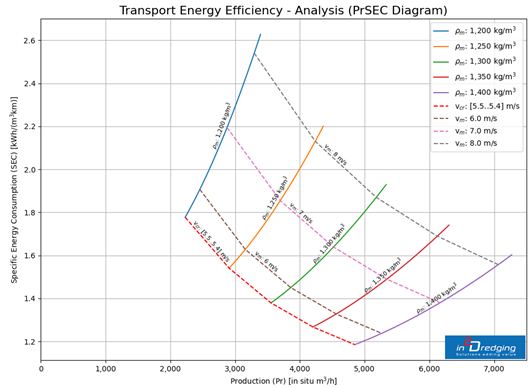
2. Go Digital
Going digital has the following advantages:
- Working from home instead of travelling to the office on a daily basis.
- Meeting online instead of flying around the world.
- Creating a digital twin to ensure project success.
- Monitoring dredging offline.
Tip: Process and visualise dredger data using i2D’s Equipment Performance Review (EPR) tool to boost productivity and quality of workmanship. The team can monitor the operations on a daily basis to ensure they are energy-efficient.
The EPR graph below shows a dredger failing to reach the vacuum limit during the night shift, while the day shift wastes energy pumping water instead of soil.
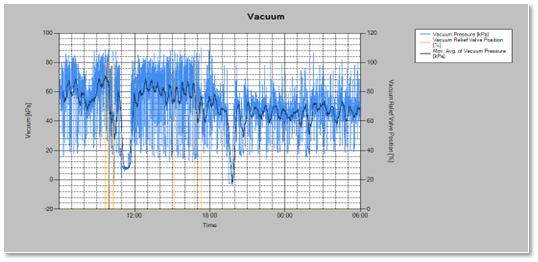
3. Use Control Systems
Control systems continuously push for the most energy-efficient process setting, whereas an operator can only temporarily outperform the control system.
4. Perform Regular Maintenance
Regular maintenance can make equipment more reliable and more energy-efficient. Regularly inspect wear parts such as impellers and teeth and replace them when their efficiency is uneconomical. Since the economic life of wear parts varies, detailed monitoring is key to preventing energy waste.
5. Invest in Energy Efficient Equipment
When it comes to energy efficiency, a small investment can make a big difference. Sometimes, we still see pump designs with only 70 % efficiency, while more modern pumps with approximately 85 % efficiency have been available since the 1980s. Modern electrical installations are simply much more energy-efficient.
6. Insulate Hot Items and Cool Spaces
Besides keeping the operator cabin at a pleasant temperature in summer and winter, certain electronics are also best kept cool to last longer. These spaces should be well insulated.
7. Test Wear-Resistant Materials
Pumps, pipes and dragheads are subject to much wear and tear. Wear-resistant materials could help extend the wear life, improve efficiency and reduce maintenance costs. The performance of wear-resistant materials is not always easy to predict, so run a test program to find out.
8. Think Green
Build with nature and create additional value with your project instead of only focusing on the value lost. Get inspired by industry-leading initiatives, such as EcoShape, for concepts you can apply to your projects.
9. Reuse Local Materials
You can get more use out of existing materials. A bit more engineering and time could make local materials, such as poorly permeable soils, suitable as reclamation materials. The key is to identify local reusable materials at an early stage and allow enough time for permitting and engineering.
10. Audit Your Site’s Energy Use
Regularly audit your site’s energy use by inviting leading industry experts who know all about best practices. The findings could make your designs and operations more energy-efficient.
Ask our environmental conscious consultants what you can or should do today!